Stacked bag sealing film developed to reduce vacuum packaging time
Issue
- Only one sheet could be sealed at a time, making the customer’s vacuum packaging operations inefficient
Features
- With the extreme melting point difference between the outer and inner layers, bags can be sealed when stacked
Application/Industry
- Vacuum packaging in general
Issue background
Film pile-ups in the vacuum packaging process reduce productivity efficiency
Although our company processes resins and our customer packages meat, we both fall under the same business category as manufacturers. Productivity improvement is a theme that will forever accompany us, and we began by analyzing the current situation and working together to find the bottleneck processes that proved to have the lowest productivity. We then discovered that products were piling up in the final vacuum packaging process. This led to a request: “Since there is a limit to how much the performance of our facilities can be improved; can’t we approach this from the film side?”
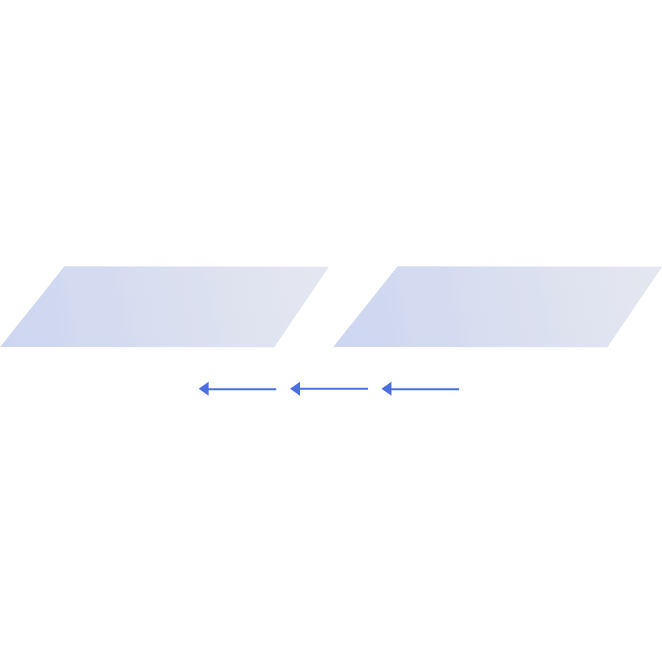
Solution
Leveraging the strengths of multilayer films to enable sealing when bags are stacked and improve productivity
A strength of multilayer films is that resins with different functions can be selected, and their thickness and order can be freely interchanged. There are two options to increase productivity: increase production speed or increase the amount of work processed at one time. In this case, we chose the latter and considered how the film could be helpful. Until then, vacuum packaging operations had to be carried out one sheet at a time, so films could not be sealed when stacked one on top of the other. We designed the outermost layer with a resin with a high melting point and the innermost layer with one that has a low melting point, with a large difference between the two. Even for five layers, this made it possible to seal them all stably, dramatically improving the throughput of our customer’s vacuum packaging process and significantly contributing to productivity.
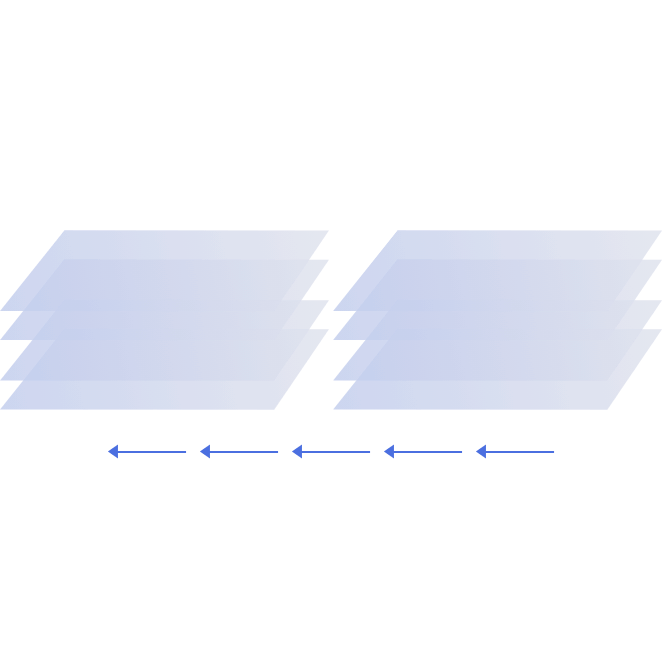