Co Extrusion Films
What is coextruded multilayer film?
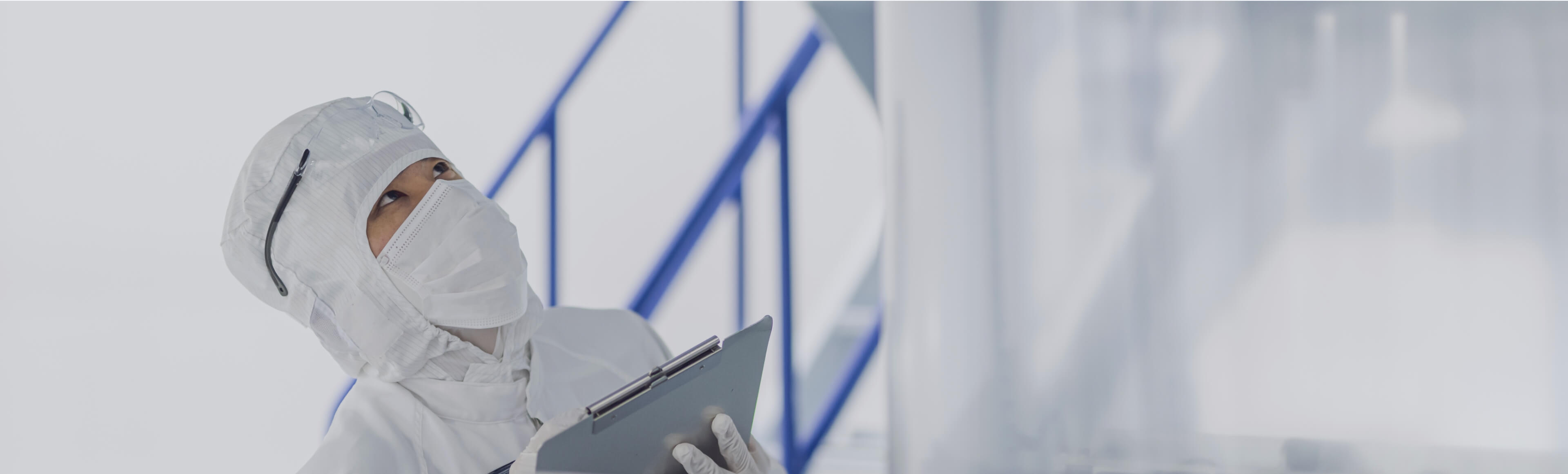
Co-extruded multilayer films with excellent inner surface cleanliness and pinhole resistance
Co-extruded multilayer films are made of melting multiple resins with different properties by layering them in a mold to form a single film.
By designing the resin type and composition ratio, various functions can be added to a single film, such as heat sealability, flexibility, heat resistance, cold resistance, pinhole resistance, and gas barrier properties, according to the customer's required performance.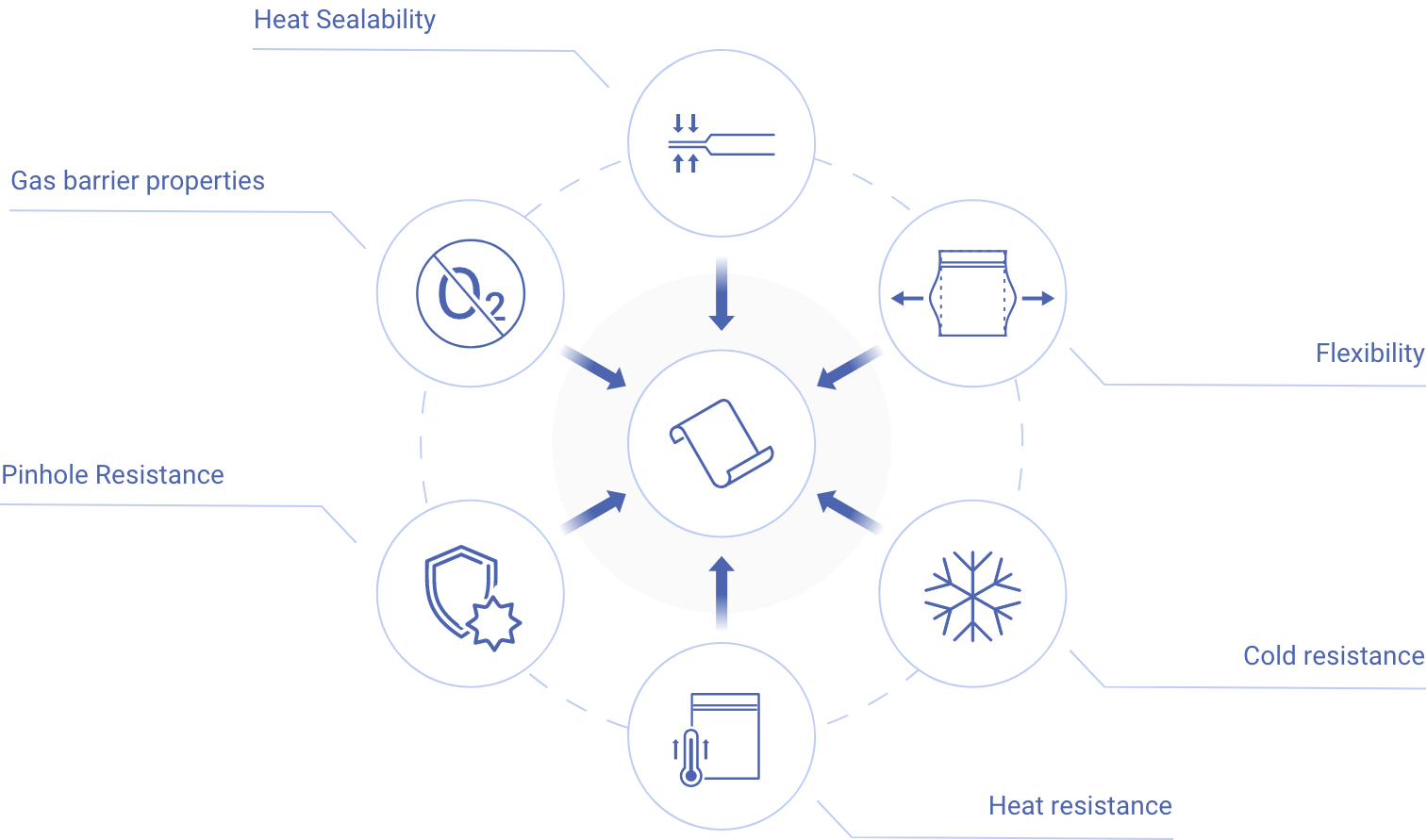
Advantages of Manufacturing with Co-Extruded Multilayer Films
In co-extrusion blown film production, the inner surface does not come into contact with the outside air, resulting in an aseptic and hygienic film.
This is why it is widely used in the medical and food industries.-
Transparency
-
Moisture Resistance
-
Waterproofing
-
Chemical Resistance
-
Oil Resistance
-
Cold Resistance
-
Oxygen Barrier
-
Aroma Retention
-
Odor Prevention
Flexible and Pinhole-Resistant Films
Friction pinholes, caused by contact between bag folds and cardboard surface, can cause air leakage and liquid spills, contaminating the contents and surrounding area.
Co-extruded multilayer film is a non-oriented, flexible film that is less prone to folding and has fewer "friction pinholes". This is a key advantage of this type of film.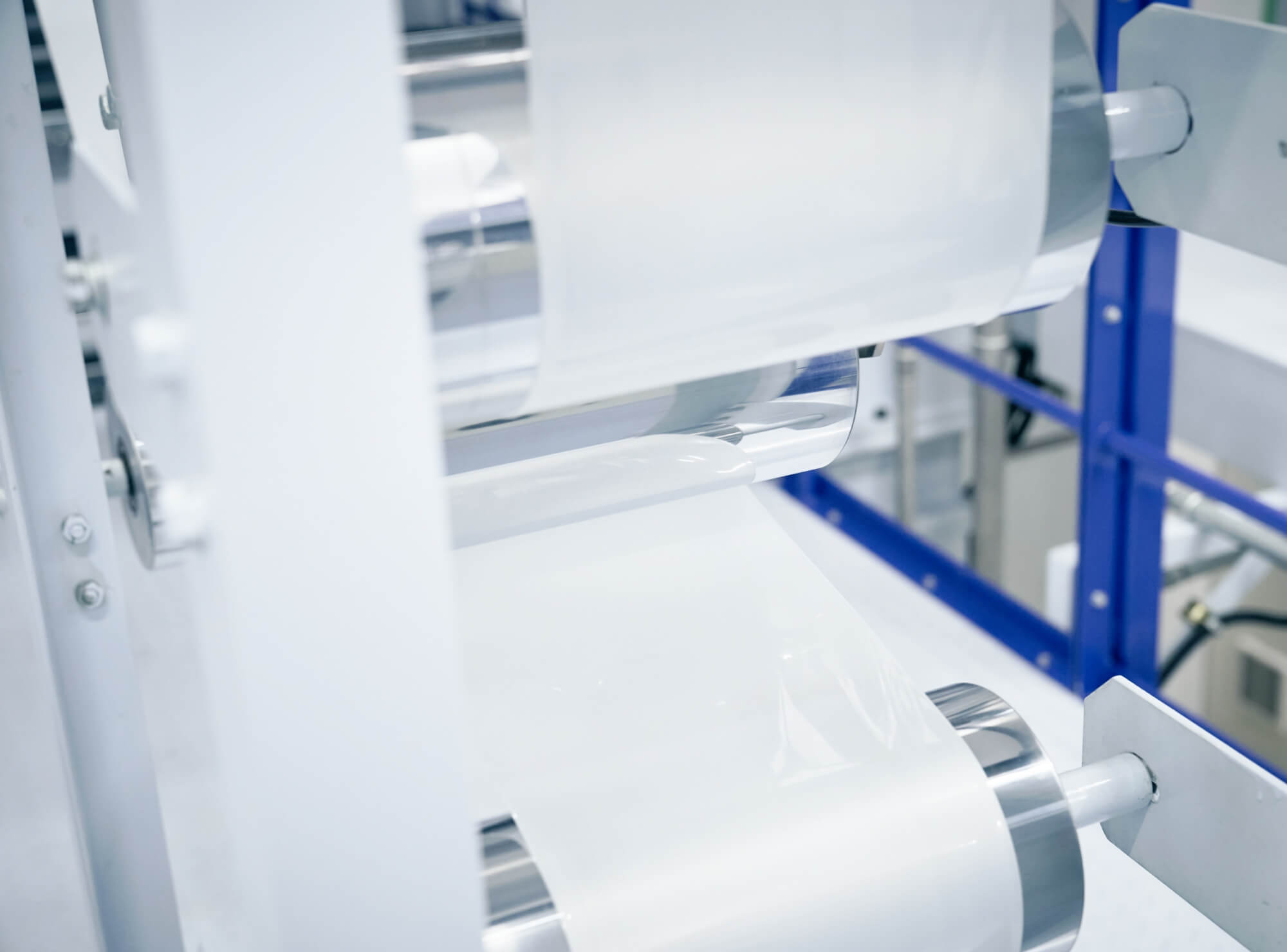
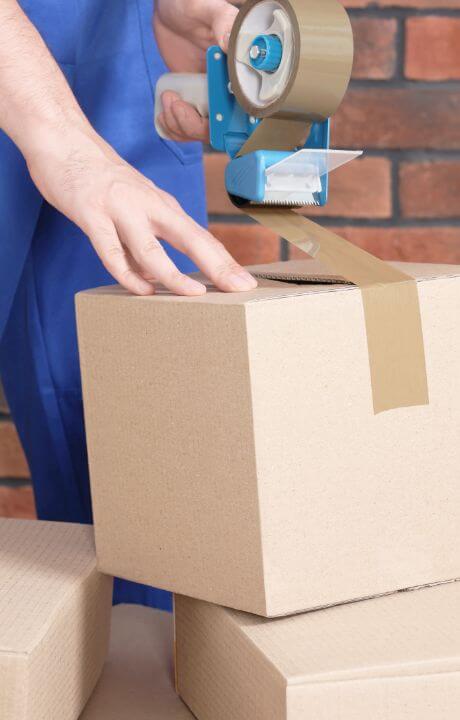
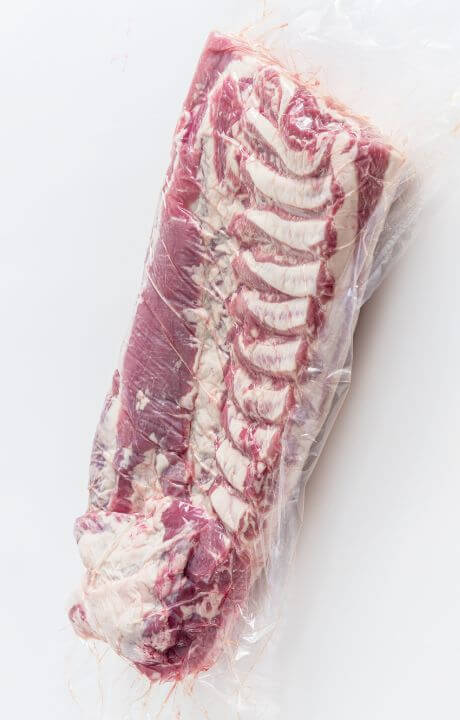
Advantages of manufacturing with coextruded multilayer films
Co-extruded multilayer films offer the advantage of tailor-made functionality for diverse applications.
While lamination involves bonding films of standard thickness, making it challenging to adjust the ratio of specific layers, co-extrusion technology enables precise control over layer ratios. This versatility allows for the creation of films with precisely tuned properties to meet the specific requirements of various industries. In the food packaging sector, co-extruded multilayer films deliver essential properties such as safety and gas barrier performance. For medical applications, safety, heat resistance, and strength are prioritized. And in the electronics industry, anti-static properties and cleanliness are crucial. The ability to seamlessly integrate these diverse functionalities into a single film is a key strength that has earned co-extruded multilayer films widespread recognition and continued support across a broad range of industries.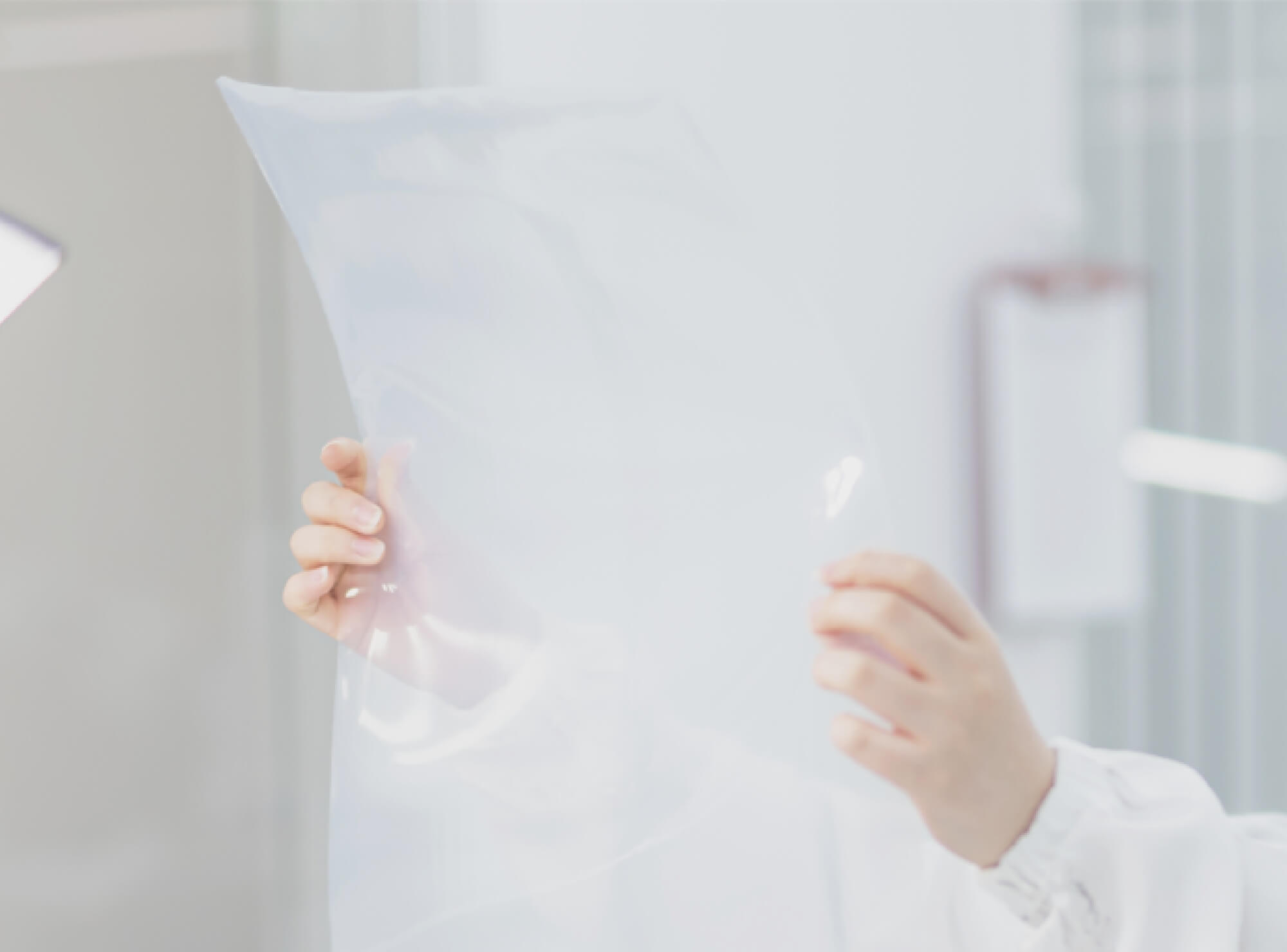
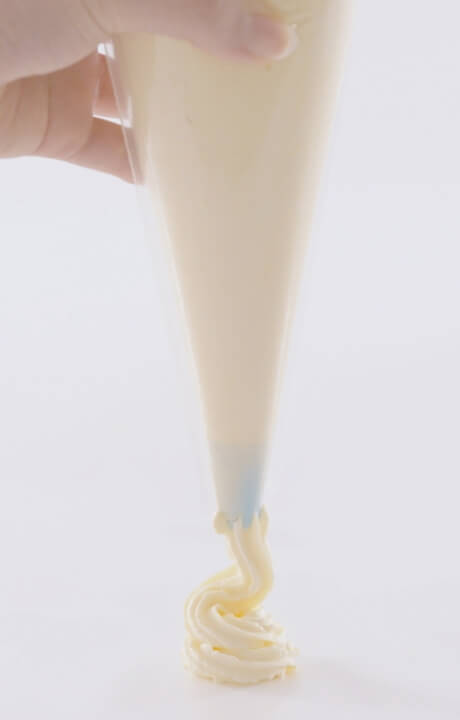
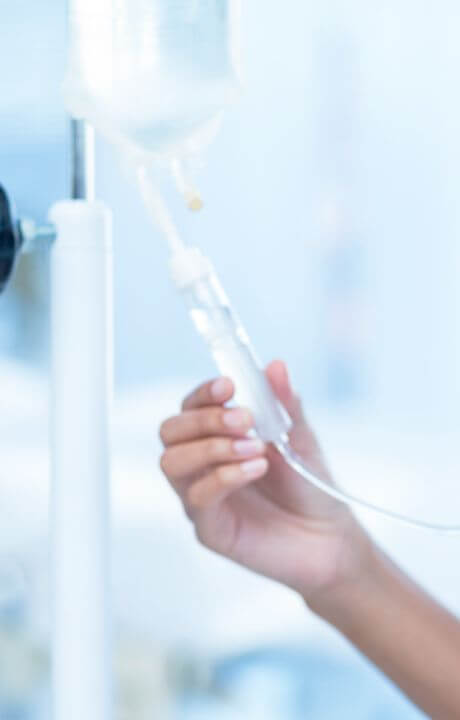
Multi-layer film produced with minimal labor and low impact on the environment
Laminated multilayer films are made by first extruding raw materials into a base film (single-layer film). These base films are then laminated together with adhesive in a laminating plant. Co-extrusion, on the other hand, is a more environmentally friendly process that produces multilayer films in one step from raw materials, without the need for a base film. This eliminates the use of adhesives and the associated organic solvents, which can remain in the film.
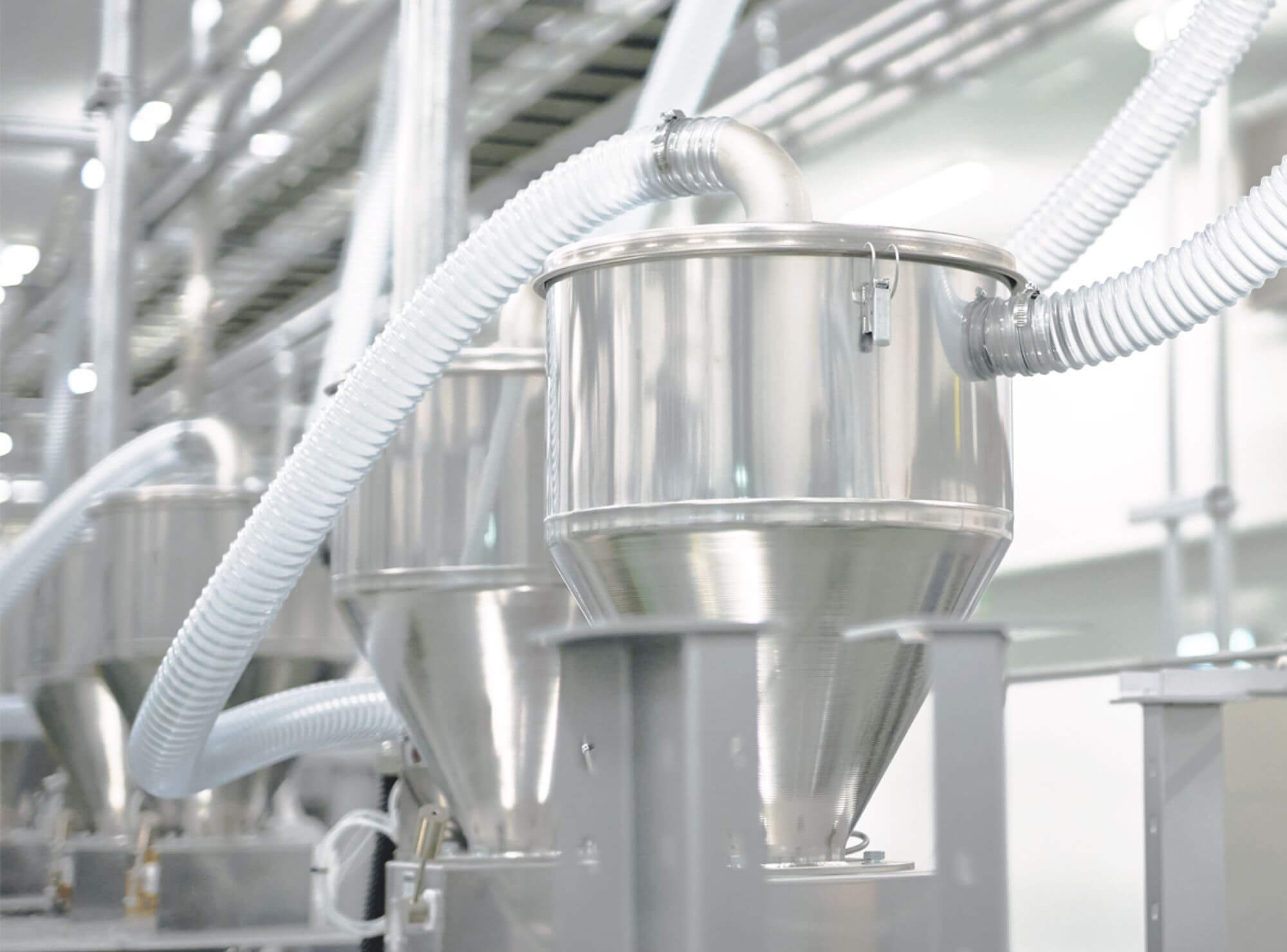
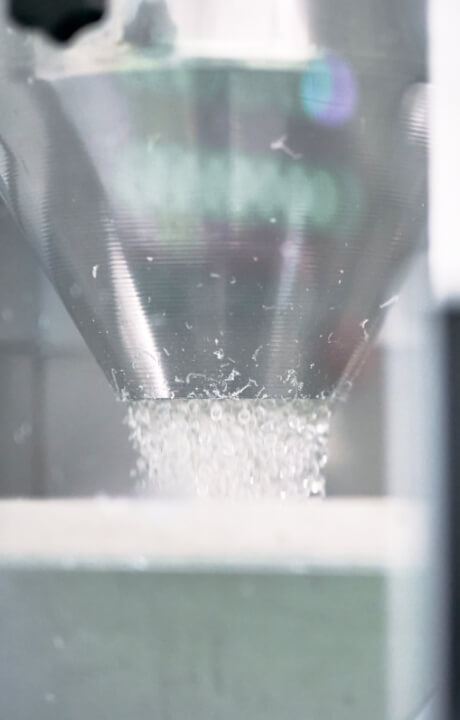
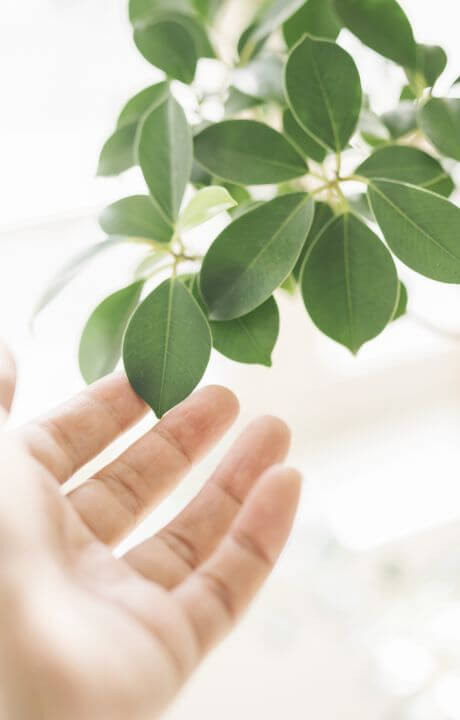
Comparison of Co-extruded Multilayer Films and Laminated Multilayer Films
Table can swipe left or right
Co-extruded multilayer films
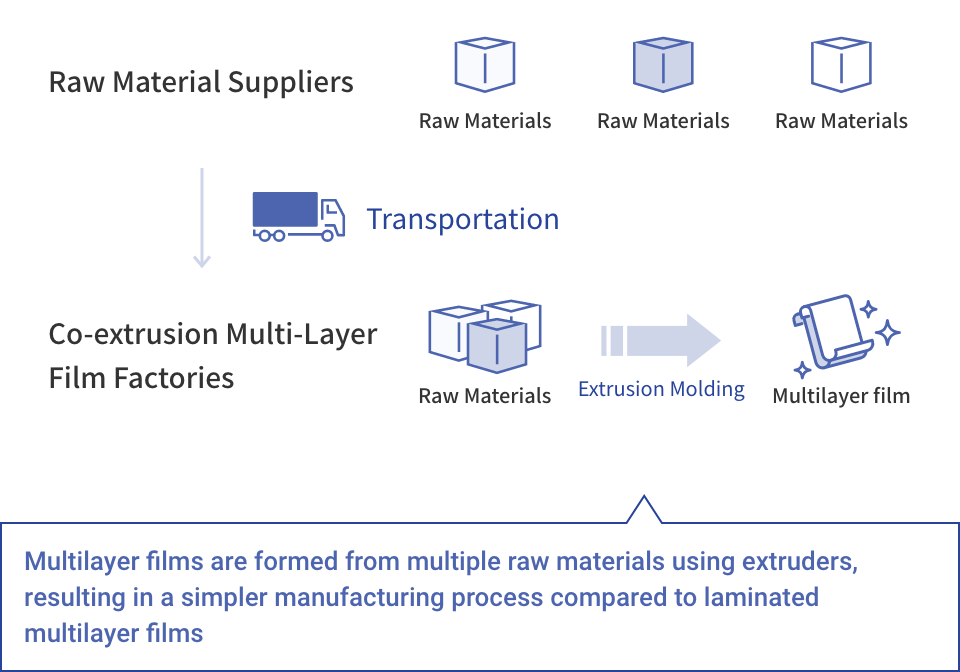
Laminated multilayer films
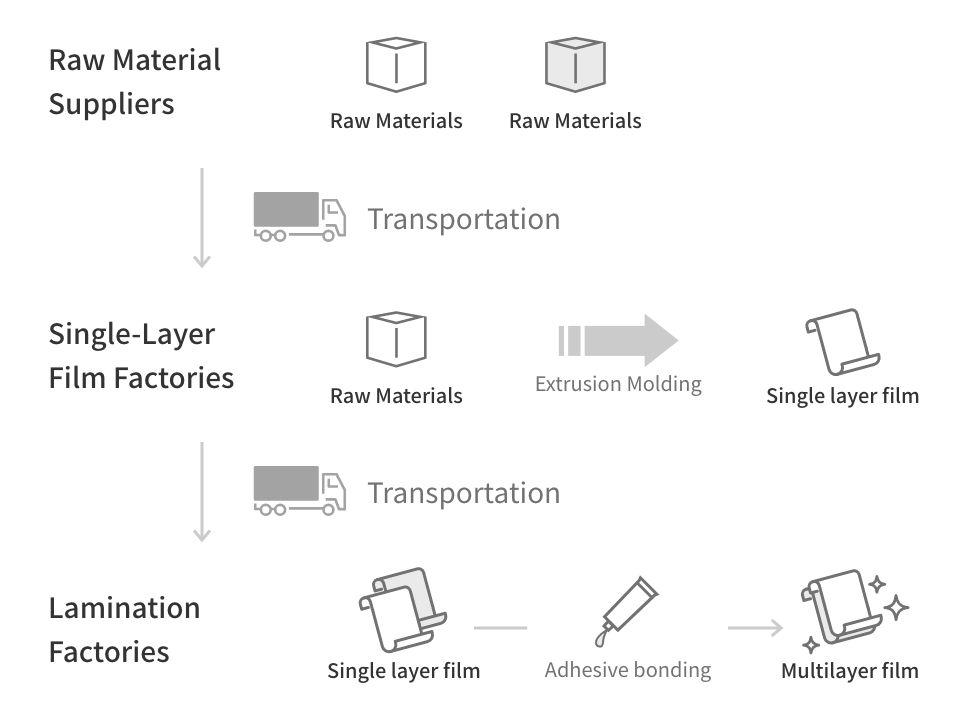
- Molding method
- The raw material pellets are melted and layered in the mold in a one-step process.
- Manufacture by laminating two or more films (substrates) using adhesive.
- Features
- Non-oriented film is soft and flexible with excellent pinhole resistance.
- Color photo printing is possible.
- Advantage
- The resin and layer ratios can be easily adjusted to meet specific needs.
- Layering of metals such as aluminum foil and paper is also possible.
Disadvantages of Co-extruded Multilayer Films
- Mold design is complex due to the simultaneous extrusion of multiple resins.
- Advanced molding techniques are required to adjust thickness and layer ratios.
- There are limitations to film printing. Color photo printing is difficult, and the production process results in "surface printing" (printing on top of the film).
Co-extrusion multilayer film manufacturing process
Co-extruded multilayer film is a type of film created through extrusion molding. It's made by melting two or more types of plastic and joining them in a mold to form a multilayer structure.
Extrusion molding is a continuous process where molten plastic is forced through a mold, shaping it into a desired cross-section. It consists of three steps: melting the raw material → extruding it from the mold → cooling and solidifying. "Co-extrusion" refers specifically to the use of two or more extruders (machines that melt plastic) to create multilayer films in a single mold.
Three types of coextrusion multilayer film manufacturing methods
-
Water-Cooling blown film method
This manufacturing method involves extruding a tube and then rapidly cooling it with water. This rapid cooling process produces a transparent film. Additionally, the inside of the tube is not exposed to air until it is used by the customer, ensuring exceptional hygiene. This method is primarily used for packaging food and medical products.
-
Air-Cooling blown film method
This method involves cooling extruded tubes with air. It is used in applications where cleanliness is crucial, such as for displays, semiconductors, and electronic components.
-
T-die method
This method involves cooling extruded film with cooling rolls to produce sheet-shaped film. This film is used for food and medical container packaging.
Products Lineup
Food-grade
-
CANS® Barrier 7
A seven-layer film with exceptional oxygen barrier properties and high strength
Product Features
- Gas barrier property
- Non-Curling
- Label adhesion
- High transparency and gloss
- High strength
Film Applications
Processed meat products
- Chilled pork
- Cured ham
- Salami
- Beef Jerky
Processed seafood products
- Salmon Tobiko
- Salmon roe
Others
- Mayonnaise
- Cheese
- Confectionery
-
CANS® CS-H
A versatile film suitable for a wide range of applications, including frozen foods, industrial, and electronic fields.
Product Features
- Gas barrier property
- Non-Curling
- Label adhesion
- High transparency and gloss
- High strength
Film Applications
Processed meat products (chilled/frozen)
- Ham
- Wiener sausage
- Bacon
- Seasoned meat
Processed seafood products (chilled/frozen)
- Fillets
- Kamaboko
- Negi-Toro
- Bonito Tataki
Other Refrigerated and Frozen Foods
- Pickles
- Cut Vegetables
- Mountain vegetables
- Whipped cream
-
CANS® B
A cost-effective vacuum packaging film with reliable performance.
Product Features
- Gas barrier properties
- High transparency and gloss
- Heat sealability
- Suitable for boiling
Film Applications
Processed meat products (chilled/frozen)
- Ham
- Wiener sausage
- Bacon
Processed seafood products (chilled/frozen)
- Fish fillet
- Fish paste product
Other Chilled and Frozen Foods
- Konnyaku
- Pickles
- Udon noodles
-
CANS FILM® CS-U
A film with excellent low-temperature sealing properties that allows for sealing when bags are stacked on top of each other.
Product Features
- Gas barrier properties
- Non-Curling
- Label adhesion
- High transparency and gloss
- High strength
Film Applications
Processed meat products (chilled/frozen)
- Bacon
- Roast Pork
Raw meat (chilled)
- Chilled pork
Industry
-
APTSTAT® FX
A general-purpose antistatic film with a stable antistatic effect.
Product Features
- Anti-static
- Environmental compliance (RoHS Directive / REACH Regulation)
Film Applications
Electronic Components
- Printed Circuit Board
- LCD display
- Module
-
APTSTAT® HA-V
A film that combines clean technology and antistatic properties
Product Features
- Anti-static
- Clean
- High strength
- Environmental compliance (RoHS Directive / REACH Regulation)
Film Applications
Electronic Components
- Printed Circuit Board
- LCD display
- Module
- HDD Components
-
APTCLEAN® HC-01
Additive-free clean film that prevents contamination of contents
Product Features
- Clean
- Environmental compliance (RoHS Directive / REACH Regulation)
Film Applications
Electronic Components
- Semiconductor Components
- Cleaning components
- Backlight Unit
-
APTCLEAN® HC-GS
Additive-free 3-layer clean film that is strong against friction and bending, making it ideal for precision parts
Product Features
- High strength
- Clean
- Environmental compliance (RoHS Directive / REACH Regulation)
Film Applications
Electronic Components
- Semiconductor Materials
- Semiconductor Components
- Wafer case
- Backlight Unit
For medical use
Contact us