Quality
Commitment to quality
Further Quality
and Safety.Pursuing higher quality and safety without compromise
To produce high-quality, safe films, high-quality raw materials and a thoroughly controlled, clean production
environment are essential. Shikoku Kakoh has established a specialized quality control department and management system to ensure consistent control from the selection and receipt of raw materials to product delivery. They all lead to genuine customer satisfaction.-
We comply with all relevant laws,
regulations, and other requirements. -
We strive to develop human resources
who can always think about customer wants and act accordingly. -
We pursue higher quality and safety
without compromise and aim to provide products and services for our customers’ peace of mind. -
By growing our company, we aim
to develop our community, create jobs, and also be a company that can give dreams to children. -
Finally, as a people-oriented company,
we aim to create an environment where employees can work enthusiastically.
Quality01
Quality control starting from suppliers of raw materials
For films for the food and medical fields, the safety and security of raw materials, particularly, are prerequisites. Large quantities of raw materials are brought into our factory every day, and strict arrangements with suppliers are essential for the stable production of high-quality films. We control quality from the raw material state by making detailed agreements on everything storage to handling and delivery methods.
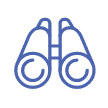
Inspections of procurement sources
We establish inspection items based on ISO standards, conduct on-site inspections for new suppliers, and document audits for our existing suppliers. Regular inspections are planned by our Purchasing Management Department and Quality Control Department and are evaluated using an inspection checklist according to the applicable scope of the business partner. For suppliers that fail the evaluation or have remaining issues, we ask them to make corrections to the extent possible, so we can strive to improve together.
Document audit
-
Inspection request
Request for self-inspection by checklist
-
Checklist confirmation
Confirm
self-inspection results -
Checklist approval
Judgment of pass/fail results based on evaluation criteria
On-site inspection
-
Inspection notice
Notice of inspection date one month prior to the scheduled inspection
-
Inspection implementation
Inspection implemented based on a checklist
-
Inspection report creation
Inspection results are summarized and reported to the inspected procurement source
Quality02
Factory design to enhance cleanliness and thorough hygiene management and insect control
Shikoku Kakoh is working to continuously improve and enhance the quality of its products by preparing the hard technology aspects of hygiene management and insect control, as well as reviewing soft technology aspects through quality management education.
Factory design to enhance cleanliness
Areas with molding machines that melt and extrude resin pellets become contaminated by machine dust and molten resin gases, resulting in high levels of particles (suspended particulates). To enhance cleanliness, we separate the area where film products are taken out, thereby reducing the presence of particles in the former. In addition, the bag-making area for films for electronics parts requiring high cleanliness is monitored, and products with particularly high cleanliness requirements are manufactured on lines equipped with clean booths to achieve a high level of cleanliness.
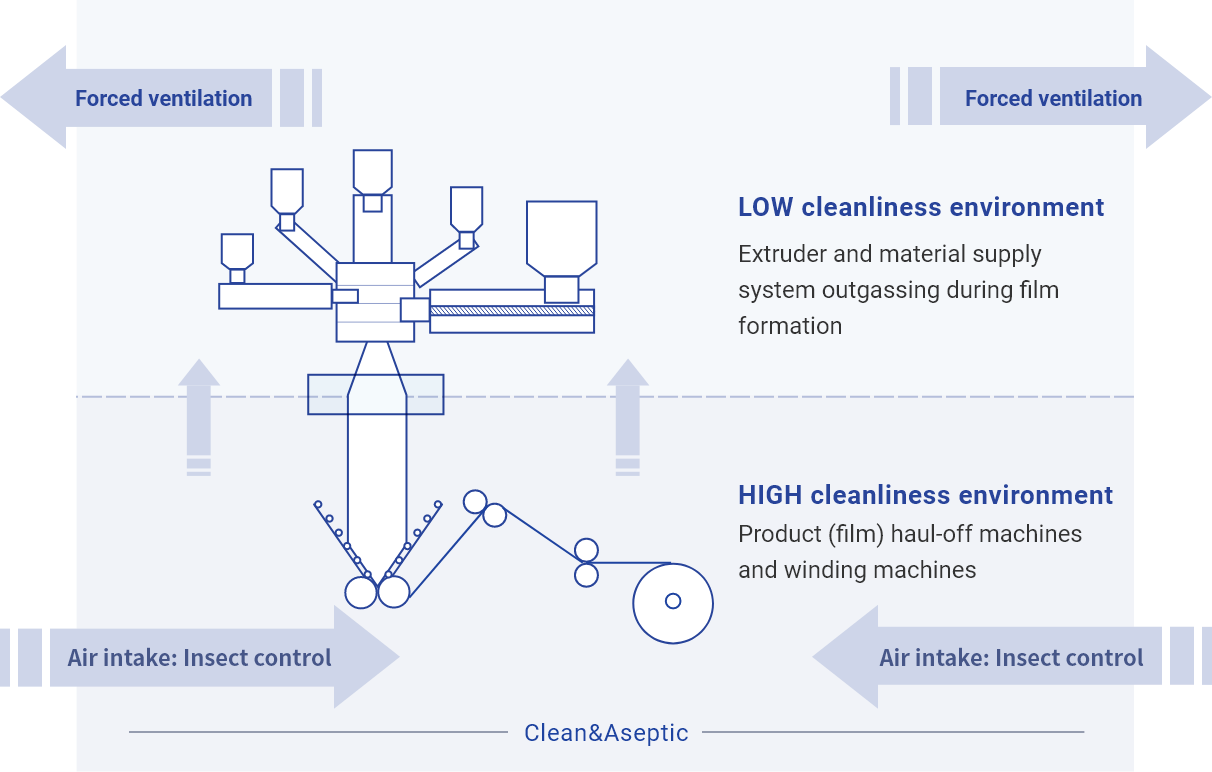
Thorough hygiene management of production areas
Before entering a production area, staff must change into clothing appropriate for the clean environment of the relevant production area to prevent contamination from outdoor or household sources and body hair and fibers from dropping. They remove foreign bodies using adhesive rollers, wash and disinfect their hands, wear gloves, and take an air shower before entering the room. In addition, bringing in mechanical pencils, staplers, and personal items that could produce foreign matter is prohibited.
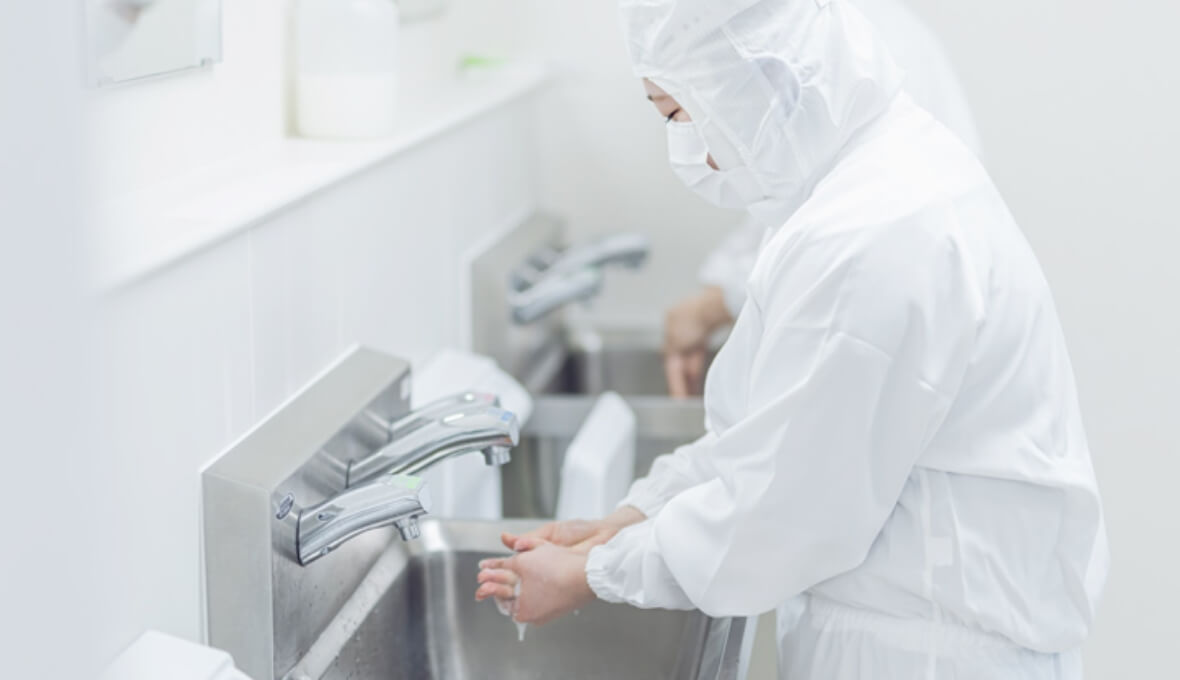
Implementing insect control and monitoring
Traps for flying and walking insects are placed in production areas, and nearby corridors, warehouse facilities, and other locations for monitoring. The number of insects caught is counted daily in areas of particular importance, and on-site inspections and countermeasures are discussed with specialized contractors. In addition, we hold monthly meetings related to insect control to discuss the status of insect trapping in each area, implementation of countermeasures, new activities, et cetera for continuous improvement. In terms of hard technology, positive pressure management is also used in high-priority areas. In addition, products are transported by an AGV (automated guided vehicle robot), which reduces the risk of bringing in insects because there is no human intervention and does not attract insects because no lighting is required.
Main insect control
- Repair cracks
- Traps for investigation
- Chemical spraying outside the factory
- Positive pressure management per area
- Interlocking passing rooms installed
- AGV (automated guided vehicle robot)
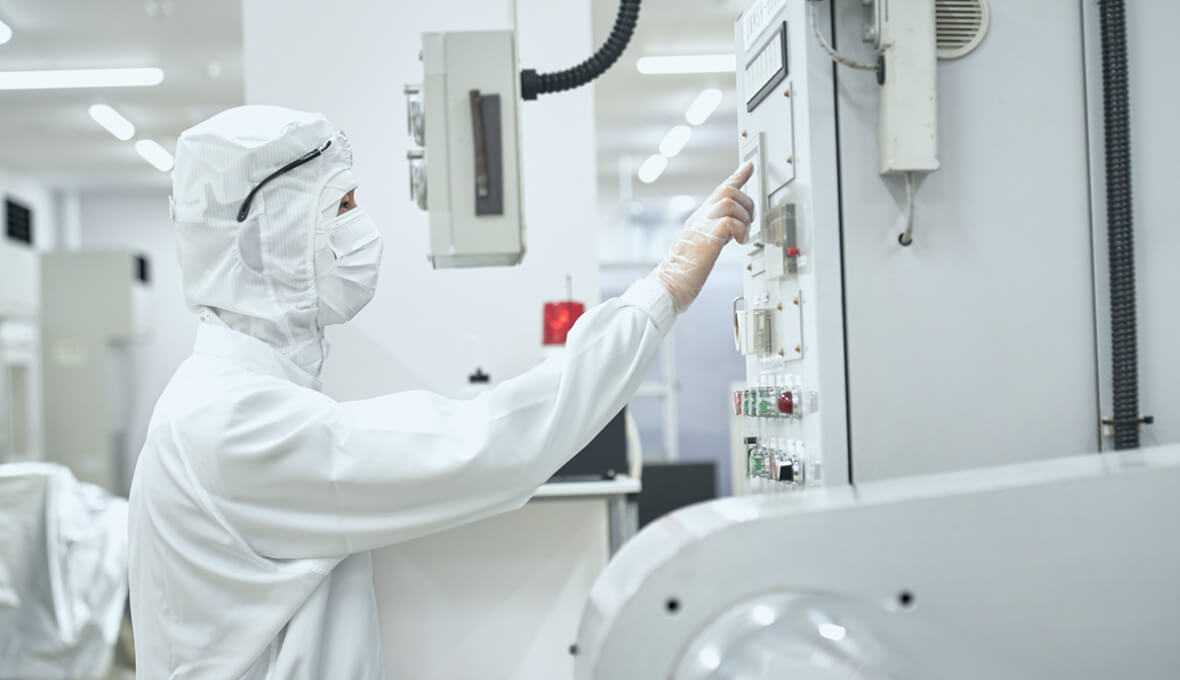
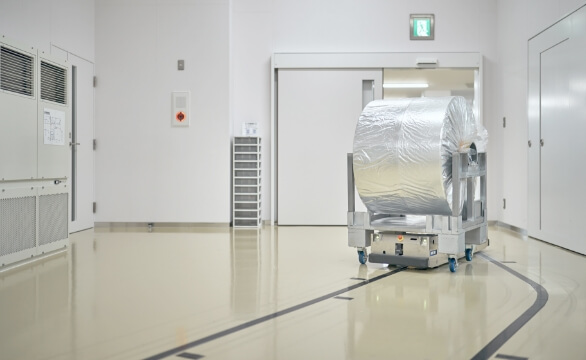
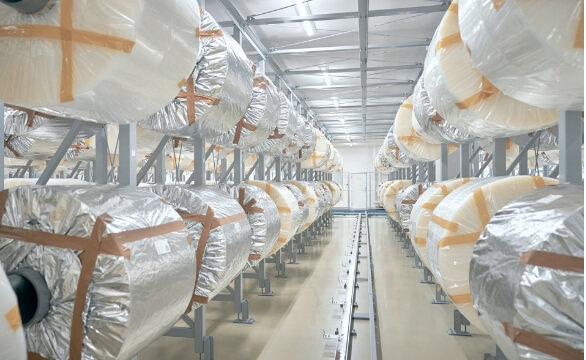
Air cleanliness measurement management
In specific production areas, high-performance filters are installed at outside-air inlets to remove suspended particles to improve the cleanliness of the area. We measure the cleanliness of our production areas every month and confirm that they are within ISO 7 (Class 10,000) or our standards.
Quality03
Pursuit and monitoring of quality and safety
By conducting raw materials control, environment measurement, and analytical testing of products, we not only confirm compliance with various laws and regulations but also constantly monitor the quality and safety of the products we provide to our customers in our efforts to deliver ongoing peace of mind.
-
PL system for
compliance with the Food Sanitation ActWe confirm with raw materials manufacturers whether the raw materials used comprise ingredients on the positive list specified in the Food Sanitation Act and obtain a certificate of conformance. To further ensure conformance, whenever necessary, we obtain certificates of confirmation issued by the Japan Chemical Innovation and Inspection Institute (JCII) for raw materials, additives, and processed products that have passed standards in accordance with the Food Sanitation Act.
-
Food Sanitation Act container
and packaging testingSince the inner surfaces of films for food use are in direct contact with food, standards and criteria are established under the Food Sanitation Act to prevent food from being contaminated by the elution of chemical substances and the like. We obtain regular analyses and test reports from external testing laboratories to determine whether our products conform to these standards.
-
RoHS directive and REACH
regulationWe confirm that the raw materials used do not contain substances regulated by the RoHS directive or REACH regulation, substances whose use is restricted by the customer, or if the content is below a threshold value. If necessary, the film is analyzed by an external testing laboratory and a test report is obtained.
-
Japanese
Pharmacopoeia testingPlastic pharmaceutical containers and packaging that containing active pharmaceutical ingredients are subjected to analytical testing to confirm that they do not contain substances or other matter harmful to the human body. An external testing laboratory analyzes our products at an appropriate frequency to confirm their conformance.
-
SDS creation and GHS
implementationWe obtain SDSs (Safety Data Sheets) for the raw materials we use from the raw materials manufacturers and check their ingredients, specific gravity, GHS (The Globally Harmonized System of Classification and Labelling of Chemicals) target ingredients, and whether there are any ingredients regulated by the Occupational Health and Safety Act, and create SDSs for our films based on this information.
-
Measurement of fine particles
in liquidFilms for electronic parts require particularly high cleanliness. Shikoku Kakoh mainly uses a liquid particle counter (LPC) to measure the number of particles to confirm the cleanliness of the inner surface of films.
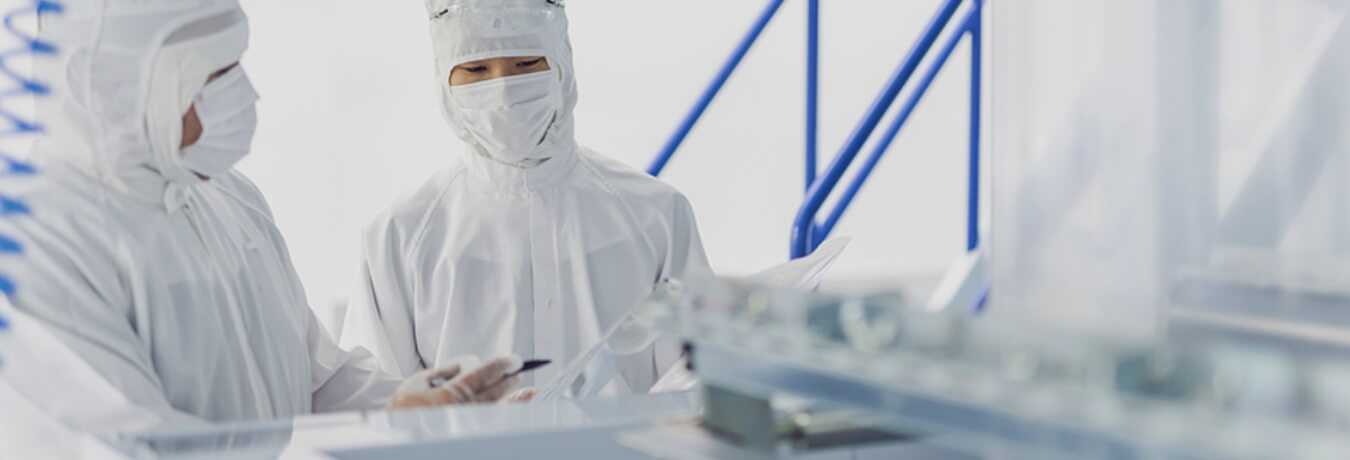
We utilize a wide variety of measuring instruments to
deliver reliable quality. We ensure that quality is constant.-
Thickness measuring machine
The film is placed on a measuring table, and the thickness (µm) is measured by the difference in height between the film and the measuring table by dropping a measuring probe.
-
Optical microscope
The cross-section of a film is magnified, and the thickness of each layer of a multilayer film is measured.
-
Tensilon universal testing machine
Tests are performed to numerically express force (N) and elongation (%), such as tensile and elongation, puncture, tear, skid resistance. The higher the number, the greater the force or elongation.
-
Haze meter
The degree of fogging (%) is measured by detecting the transmitted or diffused light when a film is exposed to light. The lower the number, the more transparent the film.
-
Thermal gradient tester
Multiple locations can each be sealed at a given temperature. By measuring seal strength (N) with a universal testing machine, the correlation between the temperature and the seal strength of the target film can be found.
-
Surface resistance meter
Surface resistance (Ω) is measured by determining the voltage from the current value flowing through a film. A low surface resistance value always discharges, making it less readily charged, while a high surface resistance value does not discharge, making it more readily charged.
-
In-liquid particle counter
Pure water is put in a sample bag, stirred, and the number of particles of a
specified size in the water is counted.The closer the number is to zero, the cleaner the water. -
Vibration testing machine
We conduct costly and time-consuming transportation testing indoors to evaluate whether packaging can protect its contents by subjecting it to vibrations that replicate truck transportation.
-
Handheld colorimeter and densitometer
By measuring and quantifying red, green, and blue, the three colors visible to the human eye, the density and color difference of colored films and printing are shown.
-
Airborne particle counter
Air is drawn into the instrument, and the number of particles of a defined size is counted. The closer the number is to zero, the cleaner it is.
-
Surface inspection equipment
This inspection equipment is designed for the extrusion molding process of raw film materials to detect foreign matter over a specified size, fisheyes, and other flaws. If necessary, defect labels are applied, and the defects are removed during the bag-making process.
-
Printing inspection equipment
By looking at differences in position, shape, and shade from a master print, the system detects print omissions, chips, and smudges.
-
Gelbo flex tester
A film is repeatedly twisted a given number of times, and the number of pinholes produced is counted to check the film’s resistance to repeated strain. The smaller the number of pinholes, the more resistant the film is to repeated strain.
-
Autoclave
This equipment sterilizes instruments and containers by applying pressure inside the equipment with high-temperature steam. We check the film’s resistance to boiling and sterilization treatment.
-
Layer thickness measuring machine
Conventionally, the thickness of each layer of a multilayer film is measured by magnifying the cross-section of the film under a microscope, but this equipment can measure the thickness of a specific layer from the film’s surface by the refraction of irradiated light.
-
Water vapor and oxygen transmission measurement equipment
A special sensor measures how much water vapor or oxygen permeates the film per day (water vapor: g/m2 · 24h; oxygen: cc/m2 · 24h · atm) in a given temperature and humidity environment.
-
Spectrophotometer
By measuring the light transmittance (%) of a given wavelength transmitted or reflected through a film, we check how well the film blocks the light that can degrade the contents, such as ultraviolet rays.
-
Barcode verification machine
The contrast and edge sharpness of barcodes are measured to confirm the overall print quality grade (ease of reading).
-
Temperature and humidity testing chamber
A given temperature and humidity environment can be created in the chamber. This is used for applications such as environmental acceleration testing of films.
-
Loop stiffness tester
This measures a film’s stiffness (N). Higher values indicate stiffer films and lower values indicate softer films.
Quality assurance system chart
Shikoku Kakoh has further established a quality assurance system to realize the concept of product safety in quality assurance. Product safety measures are implemented at the development and supply stages of each business activity to ensure product safety and prevent problems and complaints. The system also stipulates appropriate responses if problems or complaints occur or are likely to occur.
Table can slide
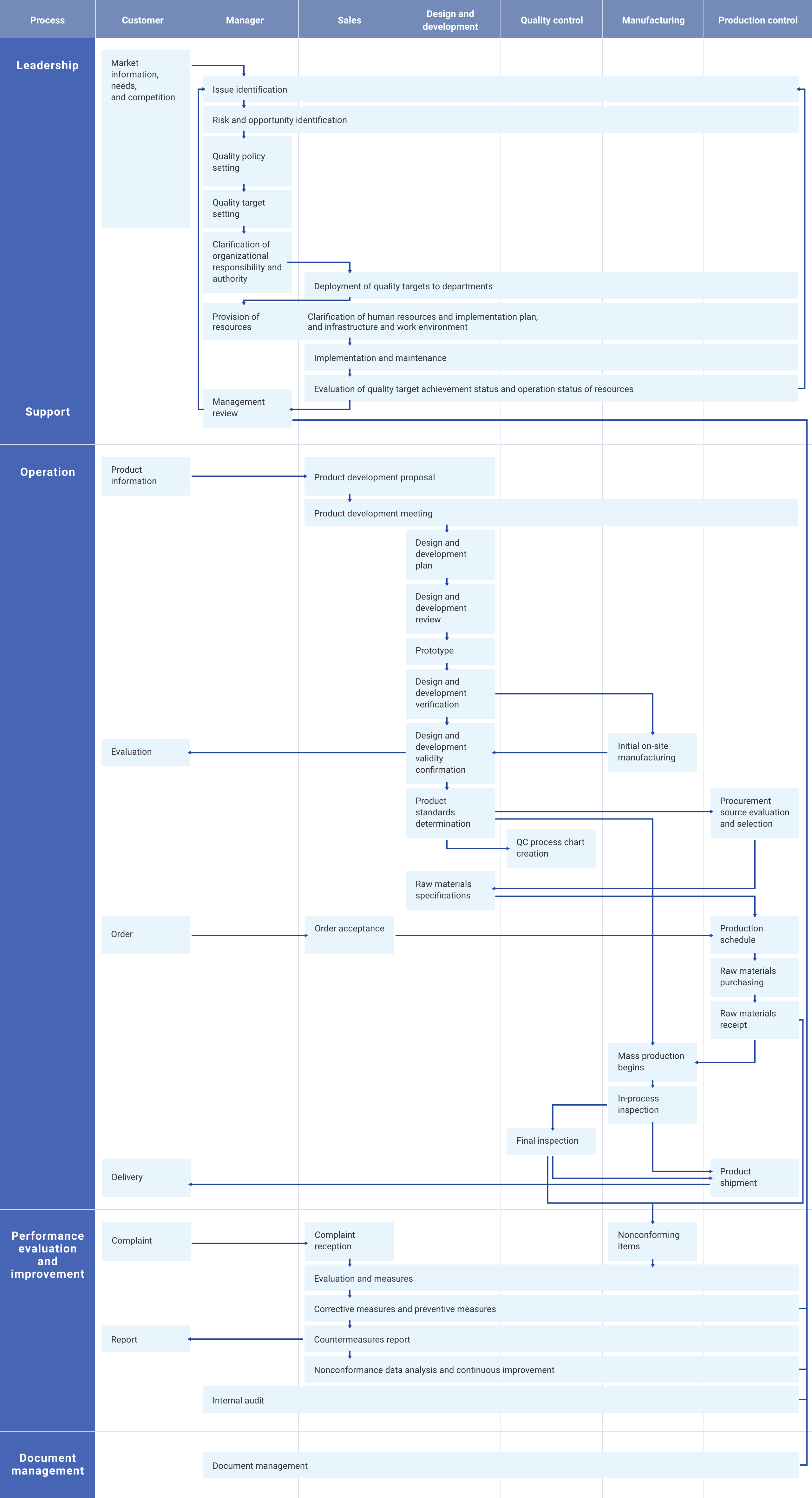
Contact us